Installation Resources to Help You Deploy Flap Barriers Faster
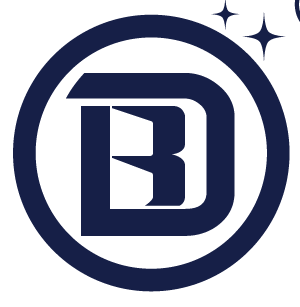
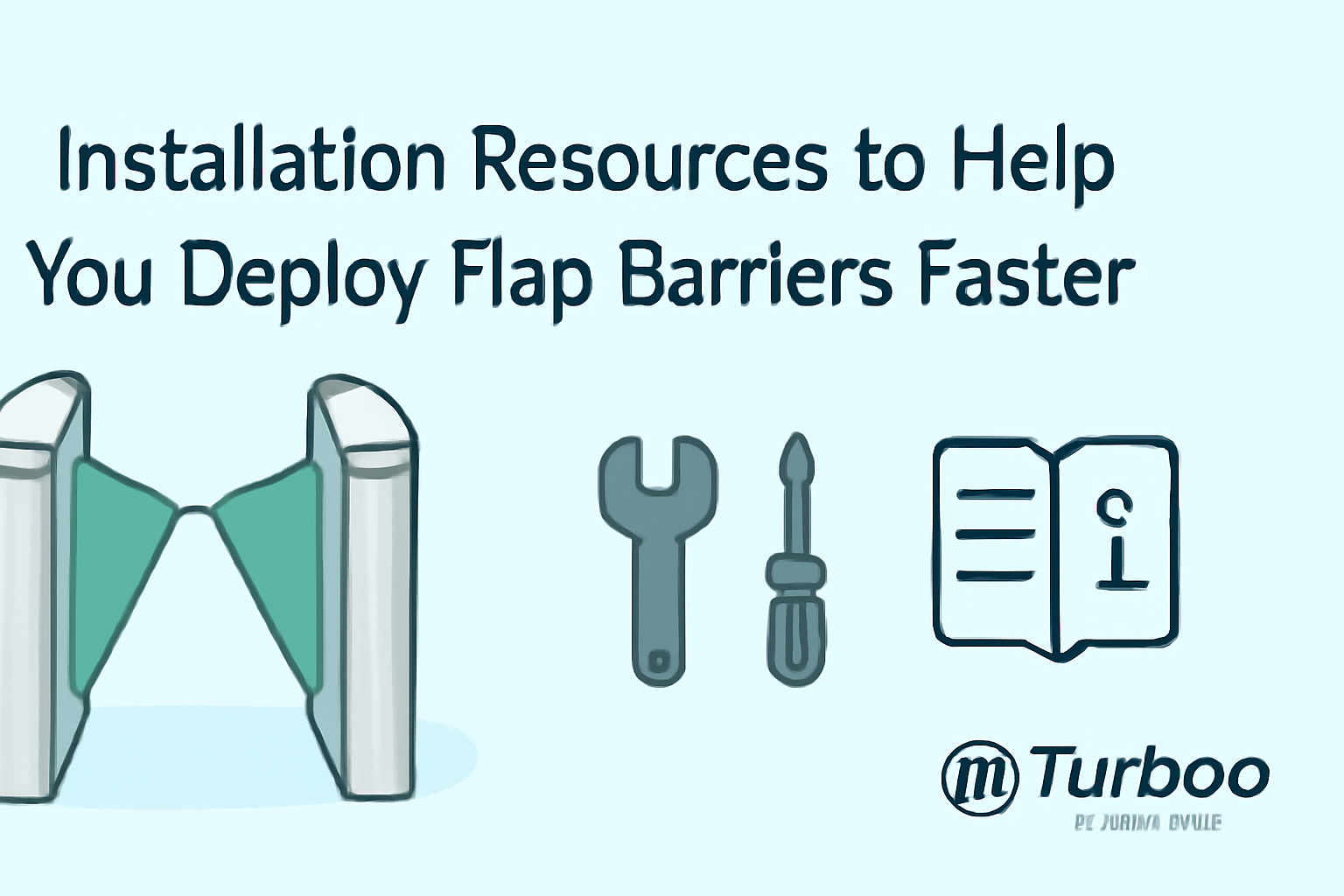
Flap barrier installation can be smooth—or a complete mess. It all depends on what resources your team has before the work begins. When project managers and installers don’t have access to the right tools, instructions, and support, things get delayed. Timelines slip. Errors increase. And frustration builds across the team.
Many teams start installations without proper documentation or guidance. They assume they can figure it out on the fly. But modern flap barriers are sophisticated devices. They include electrical components, motorized parts, software integrations, and safety systems. There’s little room for guesswork.
This guide is designed to help. It outlines the most useful flap barrier resources that installation teams can use to deploy systems faster and with fewer problems. These include manuals, walkthroughs, toolkits, prep checklists, troubleshooting advice, and support networks—all tailored for real-world projects.
Having access to these resources doesn’t just make the job easier. It improves outcomes. Installers work faster. Mistakes are caught early. And systems function better from day one. It’s a smarter way to approach every installation.
If you want your next project to finish on time and without headaches, this guide gives you exactly what you need. Every resource here is aimed at one goal—getting your flap barriers installed faster and more effectively.
The Value of Clear Installation Manuals
One of the most critical flap barrier resources is the installation manual. This may seem obvious, but not all manuals are created equal. A well-designed manual can guide your team through the entire deployment process with clarity and precision. A poor one? It leaves you guessing, which leads to delays and costly mistakes.
Good installation manuals include more than just technical specs. They provide real-world instructions. They show how to unpack and handle the equipment.
More importantly, manuals clarify compatibility. Many flap barrier systems integrate with access control systems—like RFID readers, biometric scanners, or card terminals. The manual should clearly explain how to connect these systems and test for functionality. It should also warn about common mistakes, such as improper voltage connections or incorrect grounding.
When teams rely solely on verbal instructions or memory, errors multiply. Manuals serve as a single point of reference, helping every technician stay aligned with the project’s needs.
Before starting any install, always request or download the official installation manual from the manufacturer. For a practical example, check out this install guide that outlines the core steps for barrier setup.
Step-by-Step Guides That Simplify Complex Setups
Even experienced technicians can benefit from step-by-step guides. These documents break the installation process into manageable stages. They help structure the workday. They ensure no step gets skipped or rushed. And they’re especially valuable for new team members or subcontractors who may not be familiar with the equipment.
Step-by-step guides go beyond the manual. They offer practical sequences based on field experience. For example, they might show the correct order for anchoring bolts, setting wiring channels, and configuring entry/exit logic. They may also include prep-day checklists, post-install verification steps, and initial power-on testing routines.
The best guides are formatted for ease of use. They use short sentences, active language, and clear transitions between tasks. Some even include tips for reducing installation time or spotting common pitfalls. For teams installing multiple lanes or high-volume systems, these guides can significantly streamline the workflow.
Step-by-step guidance is also useful for project managers who need to track progress. They can use it to schedule technician tasks, set checkpoints, and estimate timelines more accurately.
If you’re looking to equip your team with field-proven steps, check out these detailed installation tips developed by experienced installers.
Toolkits That Support On-Site Installation Efficiency
No matter how skilled the technician, they can’t work without the right tools. That’s where a proper toolkit comes in. Having all required tools and accessories bundled together ensures the job starts smoothly and stays on track.
A complete flap barrier toolkit usually includes anchors, bolts, cable glands, sensor mounting plates, and power connectors. Some models also require special alignment tools, calibration devices, or anti-static gloves. If these items are missing or delayed, installation stalls.
The ideal toolkit isn’t just hardware—it includes instructions, quick-start cards, and sometimes USBs or SD cards preloaded with setup software. Having these items pre-packaged with the barrier shortens prep time and reduces reliance on sourcing parts from local vendors mid-install.
For teams handling large projects, having a standardized toolkit for every technician ensures consistency. It also improves speed, since techs know exactly what tools they’ll be using and how to apply them to each unit.
Kits should be verified before delivery. Each item should be checked for quality, compatibility, and completeness. If your supplier doesn’t include a standard install kit, make one yourself based on the manual and installation tips.
Proper toolkits don’t just help—without them, installations stall. They are one of the most valuable flap barrier resources a team can bring to the field.
Troubleshooting Guides for Fast Problem Solving
Even with the best planning, issues will come up. A sensor won’t respond. A flap won’t close. A reader isn’t syncing. That’s where troubleshooting resources become critical. They help technicians identify, isolate, and fix problems without losing hours on trial and error.
A good troubleshooting guide is structured by symptom. It starts with a clear problem description and then outlines likely causes and step-by-step solutions. This structure helps even junior techs diagnose issues quickly.
These guides are most helpful when they include real-world scenarios. For instance, they might explain what to do if a barrier flap sticks halfway, or if the device fails to respond after power-on. Each issue should include visual cues, electrical checks, and firmware reset instructions where relevant.
Some troubleshooting resources come in the form of interactive apps or online databases. These allow techs to search by model or error code. For distributed teams, having remote access to such resources reduces the need to call technical support for every minor glitch.
Using these aids minimizes downtime, boosts confidence, and keeps the install process moving. Every project should include a digital or printed copy of troubleshooting instructions ready on-site.
Checklists for Reliable Site Preparation
Before installation even begins, the site must be ready. Without this, even the best equipment and team can’t proceed. That’s why a site preparation checklist is one of the most essential installation aids.
This checklist ensures all conditions at the site meet installation requirements. It verifies dimensions, flooring strength, lighting, access clearance, and power supply. It also checks that all stakeholders are informed and that access control systems are ready for integration.
Using a checklist turns vague planning into structured execution. Project leads can walk the site, mark completed steps, and flag pending items. Installers know what’s done and what’s missing. Misunderstandings are avoided, and surprises are minimized.
Teams often overlook minor but critical items—like ensuring ceiling height allows for sensor alignment, or that Wi-Fi signals reach the controller. A checklist brings attention to these details before they become problems.
If your project doesn’t have a checklist yet, you can get started with this one from site prep experts.
Access to Industry-Standard Technical Support
Sometimes, no matter how detailed the manual or how thorough the guide, installation teams encounter problems that require expert help. That’s where technical support becomes essential. Access to industry-standard support channels ensures you’re never stuck for long.
Good technical support is more than just a helpdesk. It includes trained personnel who understand both the mechanical and electronic aspects of flap barrier systems. They can assist with advanced wiring configurations, firmware updates, software integrations, and error diagnostics.
Support may come in various forms. Phone-based assistance provides immediate answers during installation. Email support helps with complex issues that need detailed documentation. Online chat or remote video walkthroughs are also increasingly common and useful in field situations.
Timely support saves hours—or even days—of guessing and backtracking. It allows your team to move forward with confidence, especially when dealing with newer systems or unfamiliar configurations.
It’s also important to know where to find reliable support. Some manufacturers have direct lines, while others use third-party platforms. In either case, having support contact details on-hand before the installation begins is smart planning.
You can explore recognized deployment and support networks such as those from SIA (Security Industry Association). They offer educational material, product certifications, and technical forums to help troubleshoot and validate solutions.
Support isn’t just a backup—it’s an active part of the installation toolkit. When used properly, it minimizes errors, clarifies setup questions, and ensures long-term system reliability.
Essential Flap Barrier Installation Resources
To install flap barriers faster, smoother, and more reliably, make sure your team uses these proven resources:
- Installation Manuals – Comprehensive documents that guide every phase of setup from unpacking to wiring and calibration.
- Step-by-Step Guides – Practical walkthroughs for new and experienced installers that explain the installation sequence in simple, clear terms.
- Installation Toolkits – Packs containing bolts, alignment tools, wiring accessories, and documentation to keep the work moving without delay.
- Troubleshooting Aids – Guides that help solve common installation problems quickly, saving time and reducing frustration.
- Site Preparation Checklists – Tools that verify all site conditions are ready before the team arrives—space, flooring, lighting, access, and power.
- Technical Support Channels – Access to live or remote support that helps with complex questions, integration issues, or advanced error handling.
For additional tools and downloadable deployment support, check out this list from IFSEC Global.
Conclusion
Flap barrier installations don’t have to be slow, error-prone, or frustrating. With the right flap barrier resources at your fingertips, you can deploy systems faster, smoother, and with more confidence. From well-written manuals to detailed guides, practical toolkits, and fast troubleshooting aids, every resource makes a difference.
Success comes from preparation and access to quality information. These resources keep your installation process on track and empower your team to deliver top-quality work on the first try.
If you’re planning a project now or in the near future, make sure every installer, manager, and technician has these tools ready. They’re not just helpful—they’re essential.