How to Evaluate Flap Barrier Product Quality Before You Buy
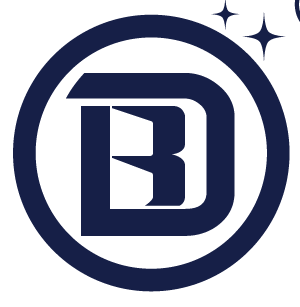
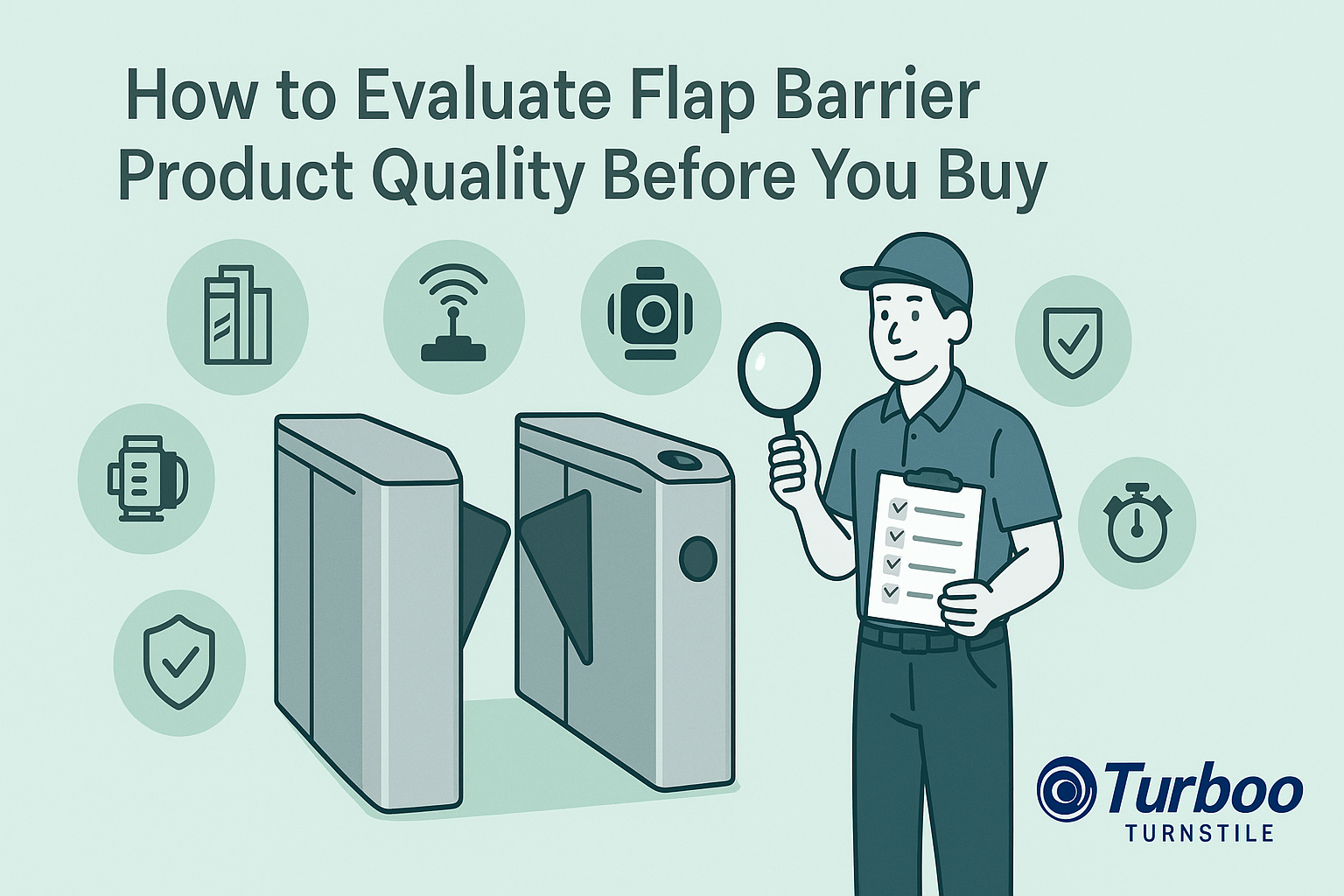
Buying a flap barrier might seem simple at first. You find a model, check the price, and place the order. But many buyers skip the most important step—making sure the product is actually built to last. That’s where things go wrong. Low-quality barriers may look fine on day one. But within months, they can start to break, jam, or create safety risks.
A good flap barrier quality check protects your budget and your site. It helps you avoid frequent repairs, angry users, or even failed inspections. With the right approach, you can spot poor design or weak parts before they become real problems.
This guide is made to help. You’ll learn what to look for, what to ask, and how to check product quality like a pro—even if you’re not an expert. Whether you’re a facilities manager, security officer, or handling access control for the first time, this step-by-step guide is for you.
What Happens When Quality is Ignored
Flap barriers take a lot of daily use. In busy areas like train stations, office towers, or schools, they open and close thousands of times a day. If the quality is low, the system won’t keep up. Jams, slow response times, or full shutdowns can happen often. And when that happens, people get stuck, delayed, or even injured.
Even in smaller buildings, a weak product causes problems. The motor might stop during peak hours. The flaps may not reset properly. Sensors could fail. These issues don’t just waste time—they raise real safety concerns. If someone pushes through during a failure, your site could be at risk.
Repairs also cost more than people expect. Cheap systems usually mean expensive fixes. Parts might not be available. Service could be slow. Every delay adds cost. That’s how buying a “budget” barrier ends up being the most expensive option in the long run.
With a proper flap barrier quality check, most of these issues can be avoided. You’ll catch bad parts, poor finishes, and lazy design before money is wasted. And you’ll make sure the product matches your needs for performance, safety, and long life.
Understanding What Makes a Flap Barrier Durable
Durability starts with the materials. A strong frame, good motor, and tough flap arms make a big difference. Barriers made with thin metal or low-cost plastic often don’t hold up. They bend, scratch, or fail under pressure. Good systems use stainless steel, aluminum alloys, or other tested metals for strength.
The internal parts matter just as much. A reliable motor should last years without overheating or losing power. The sensors should respond fast but not trigger false alarms. Even the hinges and flaps need to be tested for repeated opening and closing without breaking.
You can learn more about these parts from the vendor’s barrier durability page. It explains how different designs affect lifespan. It also shows how durability links to how well the barrier performs in real use.
Durability also depends on how the system handles wear and tear. Does it have shock resistance? Are there coatings to resist weather or dirt? Is the software designed to manage traffic spikes? A quality product answers yes to all of these.
If you check for durability before buying, you get peace of mind later. The system won’t just work—it will keep working when you need it most.
Checking for Solid Build and Smart Design
The way a flap barrier is built tells you a lot. Take a close look, and you’ll see signs of good—or bad—work. Does it have a clean finish with smooth welds and no sharp edges? Are the flaps even and straight? Is the housing solid or wobbly? These things matter.
Design isn’t just about how it looks. It’s about how it works over time. Good design means the flap opens and closes fast but smooth. It means sensors know when someone is coming—but don’t trigger false alarms. It means there’s enough room for repairs without tearing the system apart.
Smart design also helps users. Are the lights clear and bright? Is there space for different readers, like badges or phones? Can staff reset the system easily after an error? These are small things that add up to a big difference in real-world use.
Some vendors skip design work to save money. They copy other systems or use low-cost molds. That leads to gaps, loose parts, or misaligned flaps. You’ll see more jams, slower movement, and more user complaints.
Don’t rush past the build. Use your eyes and hands. Tap the housing. Watch a demo if you can. A solid system looks and feels solid. That’s one of the best signs that it’s built to last.
Why Product Testing Matters
A strong barrier on the outside doesn’t mean it’s tested on the inside. That’s why you should always ask if the product has been tested—and how. Good flap barrier makers put their systems through stress tests before they sell them. These tests check how the product holds up after thousands of uses, extreme heat or cold, or power changes.
One way to be sure is to ask about lab certification. Trusted labs like UL check products for safety and performance. If a barrier has passed their tests, that’s a strong sign it meets industry standards. They test things like heat resistance, force tolerance, and how long parts last under pressure.
You should also ask if the vendor does in-house testing. Some brands simulate years of use in just days by running barriers non-stop. Others test how fast sensors respond, or how flaps react when pushed too hard. These tests matter more than marketing words.
A good flap barrier quality check includes asking for these test results. If the vendor can’t show them, think twice. Testing proves that what looks good in the showroom will still work two years later in real life.
Know the Quality Standards
Not every barrier follows the same rules. That’s why it’s important to look for systems that meet clear quality standards. These are rules set by experts to make sure products are safe, strong, and reliable. One trusted group is ISO. They create global standards for how products should be made and tested.
If a flap barrier meets ISO standards, that’s a good sign. It means the maker followed rules for safety, materials, and testing. It also means the factory uses good processes. You’re less likely to get a faulty unit or missing parts.
Some barriers also follow local or regional codes. In some countries, access control systems must meet certain electrical or safety ratings. Ask your supplier what standards their barriers meet. If they say none, that’s a red flag.
Look for certifications printed on the barrier or listed in the manual. Things like CE, UL, or ISO show that someone independent checked the product. This step helps make sure your flap barrier quality check is based on facts—not just looks or sales talk.
Understand the Vendor’s Role in Quality
Even the best product can fail if it comes from a poor supplier. That’s why checking the vendor is just as important as checking the product. A trusted vendor makes sure your barrier is real, tested, and supported. A bad vendor might sell you a copy, skip support, or vanish after delivery.
Start with a vendor check. It helps you see if the supplier is known, if they’ve done projects like yours, and if customers are happy. A good vendor will answer your questions clearly. They’ll offer proof of past work and won’t rush you.
Also, ask where the barriers are made. Is it their own factory or a third party? Do they inspect each unit before shipping? These steps matter. They reduce the chance of broken or fake products.
Good vendors also give you training, service, and updates. That shows they expect their product to work long term. A company that offers support is more likely to care about quality. They know poor service leads to lost clients.
So before you choose a product, choose a supplier you trust. A strong vendor is part of your quality team.
Look for Proof of Field Performance
Lab tests are good. But real use tells the full story. That’s why you should always ask where the flap barrier has been used—and how it’s performed. If a vendor can show photos, case studies, or reports from clients, that builds trust.
Try to find sites like your own. If your building sees heavy foot traffic, ask how the barrier works in a busy office or transit hub. If you need outdoor use, ask how it handles rain or heat. The closer the match, the better the insight.
Ask for details: How long has the barrier been running? How often has it needed service? What did users say about it? Vendors who value quality will share this without hesitation.
If you can, visit a local site where the system is installed. Or ask for a live video demo. Seeing the barrier in action gives you clues about speed, noise, and build quality that brochures can’t show.
Field use proves that the product isn’t just tested—it’s trusted.
Know How to Inspect the Mechanism
Looking inside the barrier helps you understand what you’re buying. Most buyers focus on the outside. But what’s inside—the motor, the sensors, the circuit board—is just as important. These parts decide how long the barrier will work and how often it needs repair.
Ask if you can inspect a demo unit. Watch how the flaps move. They should open fast but smooth. No shaking or loud clicking. The motor should start and stop cleanly. If it groans or lags, that’s a warning sign.
Look at the wiring. It should be neat and clear—not messy or taped. Check if the barrier has extra protection from dust or moisture, especially for outdoor use. Ask how many opening cycles the unit can handle without failure. This is a key part of a real flap barrier quality check.
A good mechanism also has clear sensors. They should detect people fast, but not too early. If they trigger randomly, the system will frustrate users.
Even if you’re not a technician, basic checks tell you a lot. If the inside parts look strong and well-placed, the barrier will likely last longer and fail less.
Understand the Warranty and Support Policy
A product’s warranty tells you how much the company trusts its own work. If the warranty is short—or filled with exceptions—that may mean the maker knows it might break. But if the warranty is long and clear, that’s a good sign of strong quality.
Ask how long the warranty lasts. One year is common. Two or more is better. Also ask what it covers. Does it include parts? Labor? Remote support? Some companies offer software updates or extra support for a small fee. These add real value.
Support matters just as much. When something breaks, you need fast help. Can you call a local office? Is support 24/7 or only on weekdays? Ask what happens if a sensor fails or a flap stops working.
Good vendors keep spare parts on hand. That way, you don’t wait weeks for a repair. They also help train your staff to do small fixes on their own. This saves time and money later.
Warranty and support are not extras—they’re part of quality. If the company offers both, they likely built a product they believe in.
Ask the Right Questions Before You Buy
Before you make a final decision, you need to ask smart questions. These questions help confirm if the product fits your needs and if the vendor can deliver what they promise. This step is an important part of any flap barrier quality check.
Start with the basics. How many times can the barrier open and close before it wears out? What kind of maintenance does it need? Does it work with your current access system? These answers give you a clear picture of daily use.
Ask about spare parts. Can you get them quickly? Are they easy to install? If a part breaks, waiting too long can disrupt your building. A good vendor will explain how parts are stocked and delivered.
Also ask about future updates. Will the software stay current? Can the system be upgraded later? If it can’t grow with your needs, it may cost more in the long run.
Use the buying guide to help form your questions. It covers what many new buyers forget. By asking the right things now, you avoid trouble later.
Spotting Red Flags in Product Quality
Sometimes, it’s what you don’t see that matters most. Poor quality often hides behind shiny metal or good marketing. So you need to look deeper. If specs are vague or missing, that’s a bad sign. A strong product comes with full details.
Check the finish. If the housing feels light, dents easily, or shows rough edges, the rest of the unit may be weak too. Touch and sound can tell you a lot. Tap the side. Does it rattle? Is the flap loose? These small clues add up.
Documentation is another clue. A quality product comes with clear manuals, install guides, and service instructions. If these are missing—or written poorly—it may mean the company didn’t invest much in product care.
Avoid vendors who rush you. If they won’t answer questions or say “just trust us,” walk away. Trust is earned through facts, not pressure.
Spotting red flags takes a little time. But it protects you from big mistakes.
Balancing Cost with Long-Term Value
It’s easy to focus on the price tag. But cost and value are not the same. A lower price now can mean higher costs later—in repairs, downtime, or full replacement. That’s why your flap barrier quality check should look at total value, not just price.
Think about how long the barrier will last. Will it still work well in five years? What will it cost to keep it running? If one system costs more but lasts longer, it may be the better deal.
Also consider service. Will the vendor help you if something breaks? Will updates keep the system running smoothly? These things matter more than saving a few dollars up front.
Value also includes ease of use. A system that staff can run easily saves training time. A system that rarely breaks keeps users happy. These hidden wins often make the biggest difference.
Smart buyers know it’s better to pay a little more for a product that works—and keeps working. That’s the true measure of a good deal.
Flap Barrier Quality Check: Quick Checklist
- Confirm the frame is made from strong materials like stainless steel
- Check the motor, flaps, and sensors for smooth movement and solid feel
- Ask for test results from labs or in-house trials
- Look for ISO or CE certifications for quality and safety
- Use a vendor check to confirm supplier reliability
- Get field reports from similar installations or projects
- Inspect inside wiring and layout—avoid messy or loose parts
- Ask for warranty length and what it covers
- Review spare parts availability and update options
- Watch for red flags like poor manuals or rushed sales pressure
FAQs
Q1: What materials are best for flap barrier durability?
Stainless steel is the most common and reliable. Avoid barriers with thin metal or plastic shells for heavy use.
Q2: Can I do a quality check without technical skills?
Yes. Basic things like flap movement, build finish, and documentation can be checked easily. Use the checklist to guide your review.
Q3: How do I know if the motor is good?
It should move smoothly, quietly, and respond quickly. Ask for cycle test data or a demo if possible.
Q4: Why do some systems fail so fast?
Many fail due to weak motors, bad sensors, or poor build. Low-cost units often cut corners on parts or testing.
Q5: Is lab testing really necessary?
Yes. Labs like UL simulate real use. Their tests prove the product can handle stress, time, and wear.