Understanding Flap Barrier Certifications: Safety & Compliance
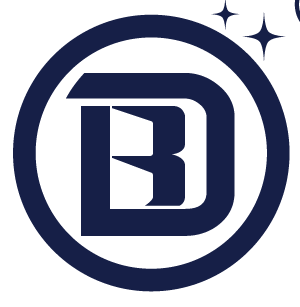
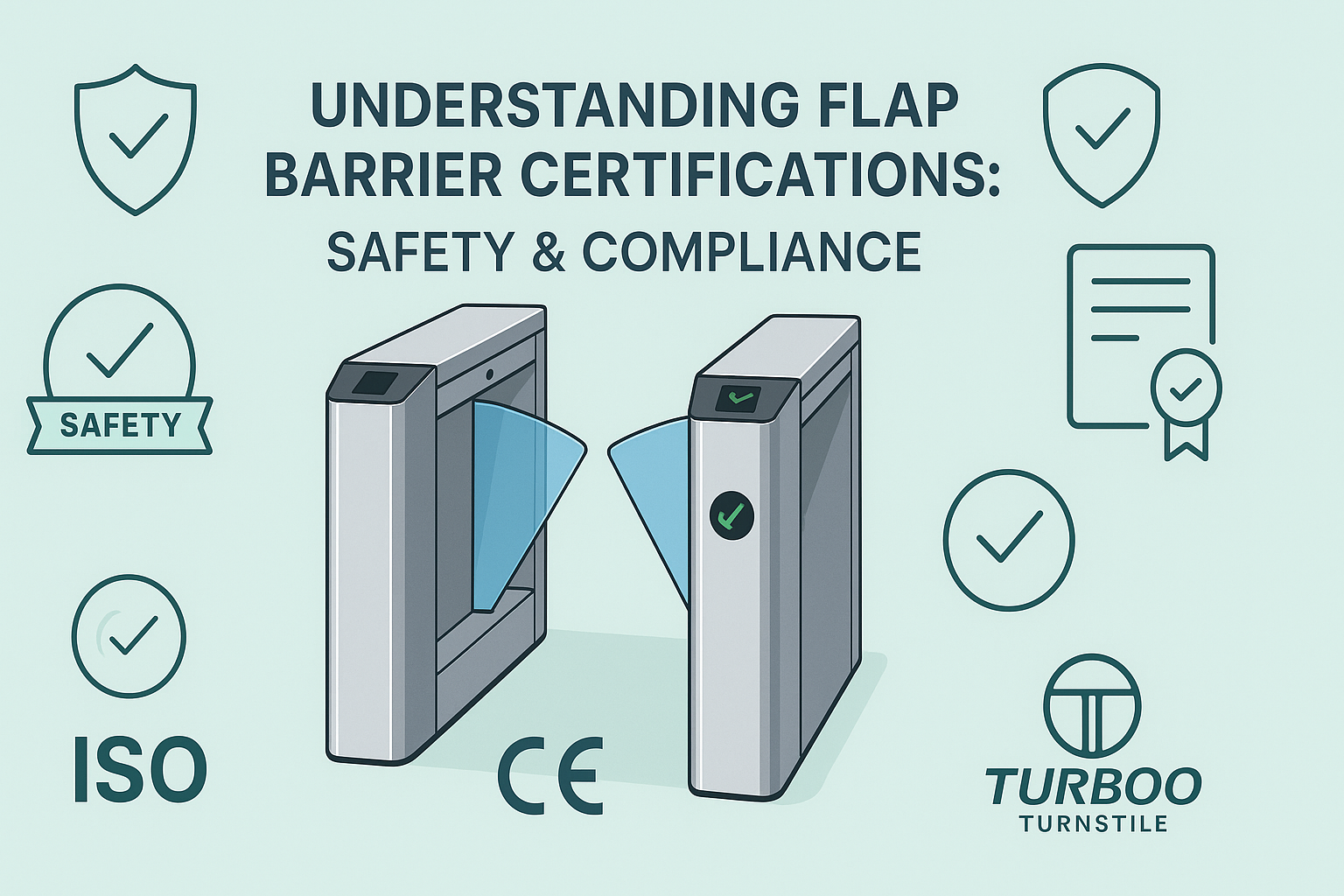
Start by highlighting that certifications prove a flap barrier meets safety and legal standards. Grab attention by stating that using uncertified gates can risk safety and cause legal issues. Build interest by promising to explain key certifications for flap barriers. Create desire by showing how knowing these certifications helps in smart purchasing and compliance. End with a statement that this article will make flap barrier certification clear and practical.
What Flap Barrier Certification Means
Flap barrier certification defines a formal process. It confirms that a gate meets industry safety standards and legal requirements. Certification applies to mechanical design. It also covers electrical components. It extends to software controls and emergency response features.
A certified barrier undergoes rigorous testing. It is reviewed by accredited bodies. These bodies verify that the product adheres to specified norms. Certification provides assurance to buyers. It signals that the barrier has passed safety approvals and compliance checks.
It covers aspects such as pinch points, fail-safe operations, and fire-safe behavior. This last ensures the barrier does not interfere with other devices. Understanding flap barrier certification is essential. It guides informed procurement decisions. It reduces the risk of legal penalties. For more details on compliance processes, see the manufacturer’s guide on flap barrier compliance.
Why Certification Matters
Safety standards exist for good reason. They protect end users from harm. They ensure that barriers operate reliably in emergencies. Without proper certification, a flap barrier may fail under stress. It may jam during a fire alarm. It may not reset correctly after a power loss. Such failures can cause injury and chaos. Uncertified barriers carry legal risks. Regulators may issue fines or orders to cease operation.
Facility managers can face liability in case of accidents. Insurance premiums may spike for non-compliant installations. Compliance certification also supports sustainability and quality goals. Certified barriers often demonstrate superior build quality.
They resist environmental factors like humidity and temperature swings. They also align with corporate governance policies. Understanding the importance of certification helps planners avoid future headaches. It underpins safe, lawful, and cost-effective access control.
CE Marking and EU Safety Standards
CE marking is a cornerstone of safety approvals for products sold in the European Economic Area. It signifies conformity with EU directives on machinery safety, electromagnetic compatibility, and low-voltage equipment.
For flap barriers, CE marking confirms compliance with the Machinery Directive 2006/42/EC and the EMC Directive 2014/30/EU. It also covers the Low Voltage Directive 2014/35/EU when applicable. The CE mark indicates that the manufacturer has prepared technical documentation. It shows risk assessments and test reports. These confirm that the barrier meets essential health and safety requirements. Installing CE-marked barriers ensures legal placement in EU markets.
It also facilitates cross-border procurement for multinational companies. Facility planners can rely on CE marking to shortcut certain local approvals. They know that the product has passed rigorous EU safety standards. For a deeper dive into the CE marking process, refer to the official EU guidance on CE marking.
ISO Standards for Flap Barriers
ISO standards provide globally recognized benchmarks. They cover quality management, environmental management, and risk assessment. For flap barriers, the most relevant ISO standards include ISO 13849 for safety-related parts of control systems and ISO 12100 for risk assessment and risk reduction. These standards guide manufacturers in designing barriers that minimize hazards.
They require systematic identification of potential failure modes. They demand verification of safety functions under normal and abnormal conditions. ISO 9001 certification further ensures consistent quality management in manufacturing processes. Adherence to these ISO standards reflects a commitment to continual improvement.
It demonstrates that the manufacturer regularly reviews and updates safety protocols. It also signals robust supplier controls for critical components. Buyers seeking high levels of operational safety often prioritize ISO-certified products. They know that such products are built under stringent quality and risk management regimes. Reviewing ISO certificates alongside technical datasheets helps compliance officers validate the integrity of flap barrier certification.
Fire Safety Approvals for Public Buildings
Fire safety certification is critical for barriers in schools, hospitals, and transport hubs. These approvals verify that the barrier does not impede evacuation during a fire. They also ensure that barrier materials resist ignition and limit smoke propagation. Testing typically follows standards such as UL 10C or EN 1634-1 for fire resistance of door assemblies.
In addition, electromagnetic compatibility tests confirm that barrier controls remain operational under the high-temperature conditions of a fire alarm. Certified barriers often include fail-safe mechanisms that retract flaps upon power loss.
They integrate with building fire alarm systems to provide immediate egress. Fire safety approvals protect lives and help buildings meet local fire codes. Installing a flap barrier without such certification can lead to code violations, fines, and forced replacements. For detailed fire testing protocols, see the manufacturer’s fire safety documentation or consult the National Fire Protection Association’s safety codes.
Regulatory Requirements Across Regions
Different countries and regions impose unique regulatory requirements on access control equipment. These regulations define minimum safety criteria, testing protocols, and installation guidelines. In the United States, the Americans with Disabilities Act (ADA) influences barrier design to ensure accessible egress. Although flap barriers are often exempt from primary pedestrian access routes, they must still provide emergency override features compliant with federal guidelines.
In Europe, the Machinery Directive complements CE marking by stipulating how machines must be safeguarded to protect users from mechanical hazards. Local authorities in major cities may require additional approvals, such as seismic resilience tests in earthquake-prone areas or ingress protection ratings for outdoor installations.
In Asia, national standards bodies often adopt or adapt ISO and IEC standards, creating hybrid certification regimes that manufacturers must navigate. Understanding these varied regulatory requirements helps procurement managers avoid non-compliance fines and project delays. Early engagement with local code officials can clarify which certifications carry legal weight in a given jurisdiction. For a deeper dive on specific norms, review the detailed guidance on flap barrier regulations provided by leading manufacturers.
Influence of Certifications on Procurement Decisions
Procurement teams rely on certifications to benchmark supplier offerings objectively. Certifications serve as a proxy for quality, safety, and reliability. When evaluating multiple vendors, certified products simplify comparison. Buyers can filter proposals by which barriers carry recognized marks such as CE, UL, or ISO. This approach reduces the risk of investing in substandard equipment.
Certification documentation also provides audit trails and technical dossiers that finance and legal teams can review. Incorporating certification requirements into requests for proposals ensures that suppliers factor compliance costs into their pricing. It also signals to the market that the buyer values long-term operational safety over upfront cost savings. Certified barriers tend to command a premium.
Yet the total cost of ownership often proves lower due to reduced liability, extended warranty coverage, and fewer maintenance incidents. In contractual negotiations, certification clauses protect the purchasing organization. They can mandate that any field modifications maintain the barrier’s original certification status. They can also require periodic re-testing after significant software or hardware upgrades. Through these mechanisms, certification drives smarter purchasing and underpins robust compliance strategies.
Long-Term Operational Safety and Compliance
Flap barrier certification is not a one-time checkbox. It underlies ongoing operational safety and compliance throughout a barrier’s service life. Certified barriers come with maintenance schedules aligned to their safety standards. Manufacturers often specify inspection intervals for mechanical components, electrical wiring, and emergency release mechanisms. Adhering to these schedules preserves the barrier’s certified status and ensures continued compliance with legal standards. In case of software updates, certified barriers must undergo regression testing to confirm that new code does not compromise safety functions.
Facilities that track certification expirations and maintenance milestones reduce the risk of equipment falling out of compliance. This proactive approach prevents unplanned downtime and avoids costly retrofits. It also reassures stakeholders—from insurers to regulatory bodies—that the facility maintains high safety standards. By embedding certification management into asset management systems, organizations transform flap barrier certification from a static badge into a dynamic tool for risk mitigation and long-term operational integrity.
Risks of Buying Uncertified Flap Barriers
Purchasing uncertified flap barriers carries significant risks. Without formal safety approvals, barriers may lack essential fail-safe features. They may jam under load or fail to retract during an alarm. Such malfunctions can lead to injuries, legal action, and reputational damage. Regulatory authorities can issue hefty fines or mandates to remove non-compliant equipment. Insurance claims related to accidents involving uncertified barriers may be denied, leaving organizations exposed to substantial liabilities.
In addition, uncertified barriers often miss critical design reviews that identify pinch points, sharp edges, or electrical hazards. They may use non-rated materials that degrade rapidly or emit harmful smoke when overheated.
In the long term, maintenance costs for uncertified gates tend to escalate due to premature wear and unanticipated failures. Retrofitting uncertified barriers to meet safety standards is usually more expensive than procuring certified units from the outset. Understanding these risks underscores why flap barrier certification is a cornerstone of responsible facility planning.
Conclusion
Flap barrier certification is a vital aspect of safe, compliant, and reliable access control systems. Certifications like CE marking, ISO standards, and fire safety approvals provide a clear framework for assessing product quality. They ensure that barriers meet safety standards, regulatory requirements, and legal obligations across diverse regions. For procurement managers, compliance officers, and facility planners, knowing these certifications simplifies vendor evaluation.
It reduces risk, enhances long-term operational safety, and protects organizations from legal and financial exposure. By integrating certification criteria into procurement processes and asset management systems, stakeholders can make informed decisions and maintain compliance throughout the equipment lifecycle.